0 引言
顶管管幕法是采用顶管技术将钢管依次顶进地层中形成管幕作为临时支护结构,然后再用开挖或箱涵顶进的方法进行地下构筑物施工的一种新型非开挖施工技术,具有安全、地层适应性好以及对周围环境影响小等优点,是地铁车站及隧道等超大型地下工程施工的关键工法[1]。
目前,我国采用顶管管幕法施工的地下工程有1984 年香港修建的地下通道、1989 年台北松山机场地下通道工程、2004 年上海中环线虹许路北虹路地道、2004 年北京地铁5 号线崇文门站、2008 年北京地铁4 号线宣武门站[2]、2008 年沈阳地铁2 号线新乐遗址站[3]、2009 年厦门杏林大桥下穿鹰厦铁路工程[4]等。上述国内已有的管幕超前支护法多结合箱涵顶进施工,平面线形为直线且长度较短,管幕顶管直径较小,且地下水影响较小,其施工技术和理论研究较为完善[5 - 8]。而目前正在建设中的港珠澳大桥珠海连接线拱北隧道首次采用曲线顶管管幕支护+水平冻结止水的施工工法,暗挖段全长255 m,平面线形为缓和曲线+ 圆曲线[9 - 14],工程规模和难度在世界范围内实属罕见,尚无类似工程施工经验可供借鉴。
因此,本文依据拱北隧道曲线顶管管幕施工资料,阐述施工中所面临的复合地层、高地下水压力以及苛刻的周围环境对工程的挑战,并对曲线顶管管幕施工的关键技术进行分析总结。
1 工程背景
1. 1 工程概况
港珠澳大桥珠海连接线拱北隧道位于珠海市香洲区,毗邻澳门,起于珠海拱北湾南部和澳门半岛东部海域的连接线人工岛,终于广东省公安边防第五支队茂盛围管理区。隧道采用双向6 车道高速公路标准,设计车速80 km/h,左线全长2 741 m,右线全长2 375 m。下穿口岸的暗挖段长255 m,采用管幕+ 水平冻结的双层暗挖工法施工,其余区段均采用明挖法施工[9 - 14]。
拱北隧道暗挖段曲线顶管管幕平面图如图1 所示。平面线形由88 m 缓和曲线与167 m 圆曲线组成;断面为卵形( 如图2 所示) ,上部平均埋深为4 ~ 5 m,总体高度约23. 8 m,宽度约22. 2 m,开挖面积达到336. 8 m2。整个管幕由36 根外径为1 620 mm 的钢管组成( 不包含0 号异位试验管) ,其中上层17 根钢管壁厚20 mm,下层19 根钢管壁厚24 mm,管间距355 ~358 mm,采用F 型接头连接,相邻管节设计最大偏转角度为0. 26°。
由于工程风险高,需要对管幕顶管涉及的关键技术参数进行现场试验,因此,在全面顶管施工前预先顶进2 根试验管( 0 号和5 号试验管) 。试验管埋深7 ~8 m,0 号试验管为附加异位管,由东向西顶进; 5 号试验管为管幕原位管,顶进方向与0 号管相反。
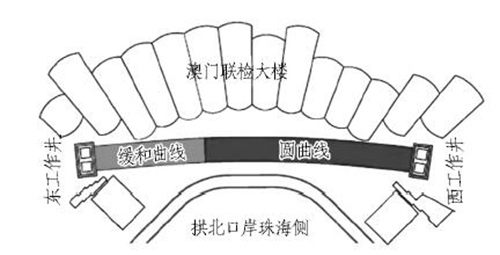
图1 拱北隧道暗挖段管幕平面图
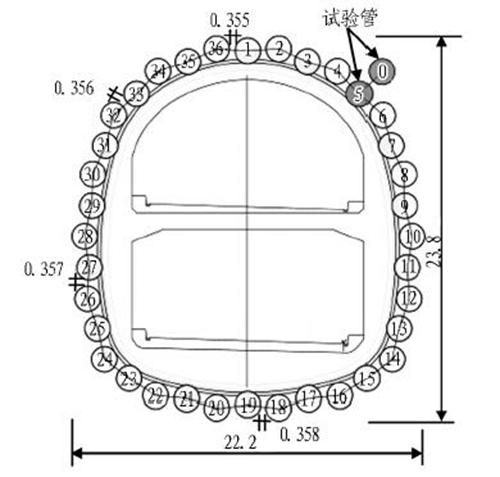
图2 拱北隧道管幕剖面图( 单位: m)
1. 2 工程地质和水文地质
隧道场区位于侵蚀堆积地貌单元,主要包括陆缘浅海、河流、滨海冲积平原3 种微地貌单元。地层从上至下依次为人工填土层、淤泥层、淤泥质粉质黏土层、粉质粉土层、黏土层、粉细砂层、中粗砂层、砾砂层、及全、强、中风化黑云母花岗岩层。其中表层海相、海陆交互沉积层厚度28 ~ 35 m,中层砂( 砾) 质黏土层厚度0. 5 ~ 8. 2 m,下伏全—强风化黑云母斑状花岗岩厚度超过20 m。
顶管管幕主要穿越人工填土、淤泥质粉质黏土、粉土、中细砂、淤泥质粉土、粉质黏土、砾砂等高压缩性、高含水量、大孔隙比、低强度的软土地层。地下水主要为含盐孔隙潜水,水位埋深浅,标高为1. 48 ~ 1. 72 m,水量丰富,且与海水连通。
1. 3 周边建( 构) 筑物环境条件
隧道沿线建( 构) 筑物及地下管线众多,给施工带来很大难度。沿线主要建( 构) 筑物有边防五支队宿舍楼、澳门联检大楼、出入境风雨廊、免税商场回廊、出入境客货通道、拱北口岸入境车行通道、拱北口岸一站式通道、广珠城际珠海站、粤海国际花园、国防公路等。沿线主要地下管线有路灯管线、电信管线、给水管、雨水管、电力管、污水管等。特别是管幕外侧距澳门联检大楼桩基最近仅1. 6 m,内侧距免税商场回廊桩基最近约0. 46 m。
综上所述,拱北隧道管幕施工主要面临以下关键难题。
1) 管幕规模目前世界最大,工程地质和水文地质条件复杂,施工穿越复合软土地层,地下水压力高( 最大约0. 3 MPa) ,对于曲线顶管施工设备性能、管节接头密封性、顶管泥浆性能以及顶管接收技术要求高。
2) 组成管幕钢管直径大、数量多、间距小,组合曲线顶管施工精度控制技术是确保管幕形成的关键。
3) 周边建筑物和地下管网密集,安全级别高,对顶管施工精度和地表沉降控制要求苛刻。
4) 周边建筑物基础、浅层建筑垃圾、孤石等障碍物众多,顶管施工障碍物处理难度大。
2 曲线顶管管幕施工关键技术
2. 1 复合地层顶管设备选型
顶管设备根据不同工程地质条件,其适用范围也不同,需要选择与之相适应的顶管设备,通常选型时要考虑以下因素。
2. 1. 1 地下水压和地层变形控制要求
当地下水压力较大、周边建筑物安全等级高时,对施工引起的地层变形控制要求高,土压平衡螺旋输送机容易发生喷涌,导致掘进面失稳,因而宜选用泥水平衡顶管机。
2. 1. 2 掘进地层特性
通常地层渗透系数大于10 - 7 m/s 时选用泥水平衡顶管机,渗透系数小于10 - 7 m/s 时选用土压平衡顶管机。同时,考虑岩土颗粒粒径分布情况,当粉粒和黏粒的总量达到40% 以上时,通常选用土压平衡顶管机,反之,则选用泥水平衡顶管机。粉粒的绝对大小常以0. 075 mm 为界。
由于拱北隧道管幕工程场区地下水压力高,如果采用土压平衡顶管机施工,存在螺旋输送机喷涌风险,并且管道直径较小,不利于渣土运输。同时,考虑到穿越的地层既有渗透系数较小的黏土层,也有渗透系数较大的砂层,顶管机需具备在不同地层中的掘进能力,且大部分地层所含颗粒粒径都在0. 075 mm 以上,拱北口岸区域建筑安全等级高,对施工变形要求苛刻。因此,宜选用泥水平衡顶管机施工。
经过多种方案比选,工程最终选用德国海瑞克生产的4 台AVN1200TC 泥水平衡式顶管设备[15],如图3 所示,包括泥水分离站等全套的辅助设备。考虑到顶管施工可能会遇到孤石、建筑桩基,以及破碎工作井混凝土墙要求,配备装有刮刀和滚刀的复合刀盘,并安装锥形二次破碎舱,可适应多种地层掘进施工。
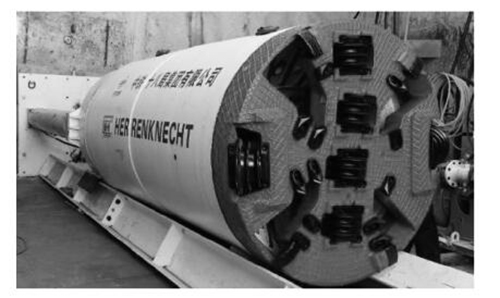
图3 海瑞克AVN1200TC 顶管机
2. 2 高水压顶管始发和接收技术
管幕顶管施工面临松散砂层和流动性较强的淤泥质层,且地下水压力较大,洞口始发止水装置和接收装置一旦密封失效,极有可能发生涌水、涌砂事故,造成洞口上部地表塌陷,殃及周围建筑物、道路及地下管线。因此,高水压条件下顶管始发和接收密封止水是必须克服的工程难题。
2. 2. 1 高水压顶管始发技术本
工程采用如图4 所示的可拆卸式折页压板双层帘布橡胶止水密封装置,其主要由折页式压板、2 层帘布密封橡胶圈、扩大钢环、连接钢环组成。顶管施工前,通过螺栓将止水装置安装于洞口孔口管上,施工完毕后可拆卸再安装于下一顶管施工位置,实现循环利用。
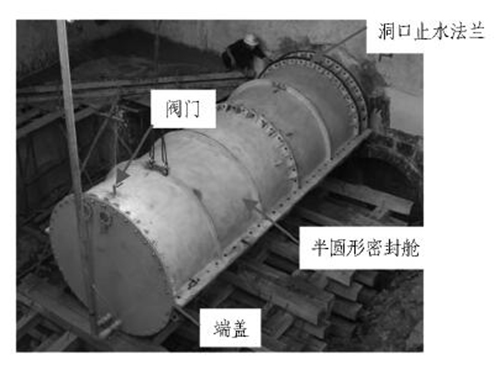
图4 顶管始发洞口止水装置
2 层止水密封橡胶圈增强了密封效果,采用多块折页式压板的设计,可根据顶管机和环板之间的距离调节折页式压板的位置,使折页式板内弧直径尽量接近顶管机外径,以减少顶管机在洞口的偏移,减小密封橡胶圈因地下水压力过大而产生外翻的可能性。密封橡胶圈能够承受0. 3 MPa 以上的高水压。
2. 2. 2 高水压顶管接收技术
为了保证顶管机能安全接收,现场施工创新采用了钢套管接收舱技术,如图5 所示。接收舱由双层橡胶圈洞口止水法兰、半圆形密封舱、端盖及附属阀门等部分组成,各部分通过螺栓拼装而成,便于拆卸和重复利用。接收舱内铺设滑板,确保机头可以平滑地从孔口管过渡到接收舱内。
在顶管机接收过程中,首先在接收端拼装接收舱,并与孔口管连接,通过注浆阀向接收舱注满泥水,然后关闭注浆阀; 然后操作顶管机进入接收舱中,舱内的泥水压力平衡地层土水压力,不但能保证接收端压力平衡,同时避免了传统接收技术引起的地层水土流失; 最后在孔口管和管道之间注入密封浆液,待浆液固化后,打开接收舱,取出顶管机,进行后续施工。
现场根据顶管深度的不同,针对不同地下水压力,采用了2 种不同结构钢套管接收舱。管幕中板上部地下水压力较小,所用接收舱由2 节拼装而成( 如图5 所示) ,内径为1 880 mm,总长5. 3 m,壁厚15 mm,每节均由2 块半圆钢套管拼装而成,各拼装面均设置密封橡胶板。
由于前期采用的接收舱在进行底部17 号顶管接收时,密封装置效果不佳,出现泥砂进入并堆积于接收舱内,各拼装面均出现漏水现象。原先使用的接收舱无法满足要求,因此,对钢套管接收装置采取了一系列技术改进措施。
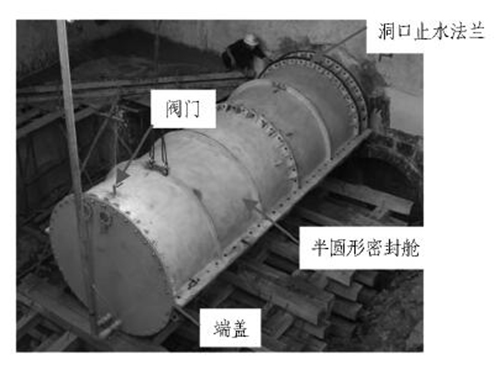
图5 上层顶管钢套管接收舱
1) 在洞口止水法兰安装注浆阀,顶管机进入接收舱后,向洞口止水装置2 道橡胶圈内快速注入聚氨酯或马丽散液浆,实现洞口快速止水。
2) 加长接收舱,并将其改为整体式,整个接收舱套筒只由2 个长7 m 的上下2 块半圆钢筒拼装而成,减少了接收舱的接合面,同时增大了接收舱能容纳的泥砂量。在接收舱端盖后部安装支架,防止高水压力导致端盖变形严重引起泄漏。
3) 拼装接合面均采用2 排螺栓加橡胶垫进行密封,同时在缝隙处涂抹锚固剂。后续中板以下的顶管均采用改进后的接收舱( 如图6 所示) ,顺利完成了高水压复杂地质条件下的顶管接收。
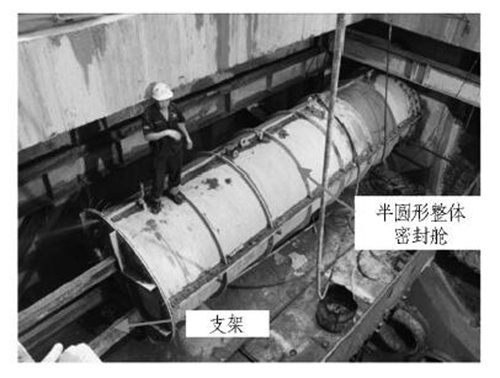
图6 高水压钢套管接收舱
2. 3 曲线顶管精度控制技术
由于管幕相邻顶管间距仅为355 ~ 358 mm,且后顶管会对先顶管道空间位置产生影响。任一根顶管轨迹偏离设计值过多时,都会影响后续冻结施工冻结圈厚度和止水效果,甚至可能占据相邻顶管位置,而使整个管幕无法形成。在充分利用AVN1200TC 顶管机自身导向系统的基础上,创新提出3 阶段小间距复合曲线顶管精度控制技术。
1) 曲线直顶。考虑到顶管曲线始发对姿态的控制要求高,可能会使顶管机偏向始发密封圈一侧。因此,始发阶段采取曲线直顶技术,顶管机沿设计曲线割线方向始发顶进,待机头完全进入土体后再开启纠偏油缸,逐步调整姿态,进而提高施工效率。
2) UNS 导向+ 人工校核。通常情况下AVN1200TC顶管机通过自身配套的UNS 导向系统实时控制顶进轨迹,主要利用掘进机机头标靶空间位置来反映轨迹变化。考虑到该工程精度要求极高,并且UNS 导向系统精度为1 mm/m,随着顶进距离的增加,其累计偏差可能会增大。因此,在顶进阶段,除了实时观察UNS 导向系统显示的机头位置外,每顶进20 m管道,采用支导线法对机头标靶的三维坐标进行1 次人工校核测量,并根据测量结果对UNS 参数进行纠偏调整[16]。
3) 三线控制法。由于接收端孔口直径只比顶管机头直径大200 mm 左右,如果接收阶段偏差太大,则会导致施工失败。为控制接收精度,制定了减速线、破墙线和顶进终止线的三线控制法。
减速线位于距离素混凝土墙50 cm 的位置,破墙线是指机头顶破素混凝土墙线,顶进终止线是机头完全进入接收舱中。该阶段主要严格控制顶管施工参数,避免大块混凝土进入接收舱或是顶进距离控制不准确,防止机头偏斜或机头破坏接收舱而导致接收失败。
0 号试验管通过以上精度控制技术,其轨迹水平、高程偏差及对相邻5 号试验管施工影响如图7—9 所示。由图7—9 可知,除少数点外,0 号管轨迹偏差基本控制在± 50 mm,邻近5 号管顶进对0 号管轨迹影响较小,最大偏差仅为12 mm。
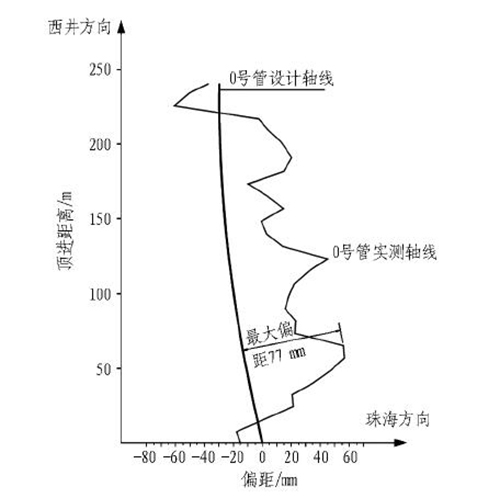
图7 0 号管轨迹水平偏差曲线
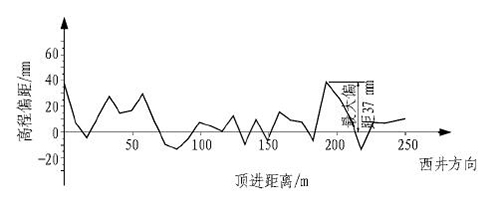
图8 0 号管轨迹高程偏差曲线
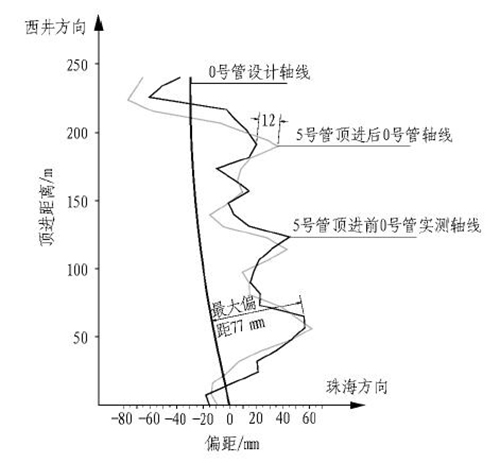
图9 5 号管对0 号管轨迹影响曲线
2. 4 管节结构与密封技术
顶管采用如图10 所示的钢管节,由20 mm( 24 mm) 厚钢板卷制焊接而成,单根长度为4 m。接头如图11 所示,为F 型承插口,通过在管节端头焊接20 mm 厚法兰和40 块20 mm 纵向加劲板形成承口和插口,以适应管节偏转的需求,管节之间采用M33 限位螺栓进行连接。为保证受力均匀,并适应曲线段内外侧不同压缩变形的要求,根据管节之间的张角,在承口与插口法兰之间安装20 mm 厚的木质垫块。同时,为保证管节间的密封性,在接头处安装2 道鹰嘴橡胶圈。
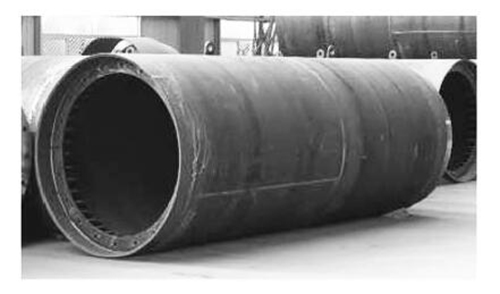
图10 曲线顶管钢管节
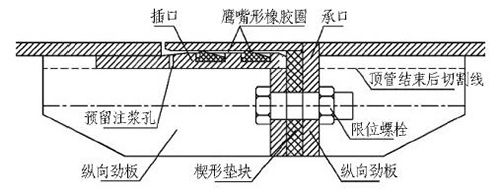
图11 F 型接头结构图
考虑到施工主要穿越的地层为粉质黏土、淤泥质粉土等软土以及中粗砂等易流失地层,若接头密封一旦失效,则可能会导致涌水、涌砂,甚至造成地表塌陷;特别是曲线顶管管节之间存在偏角,降低了接头密封圈的密封性。为验证曲线顶管接头密封能力,对其进行了室内试验,采用如图12 所示的试验系统,主要由管道组件、加载反力装置、注浆加压装置和数据采集装置组成。管道组件由测试管节、外密封套管、简化接收舱和洞口止水装置组成,各部件通过螺栓连接。
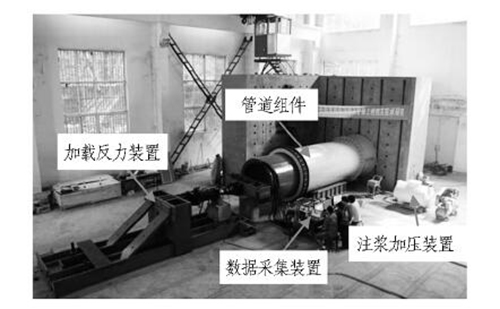
图12 室内顶管密封性测试系统
试验过程中通过注浆加压装置向测试管和外套管之间注入泥浆并加压,试验设计每一级泥浆压力为0. 1 MPa,并保压30 min。试验共测试3 种状态下管节的密封情况,分别为管节偏转0° 、0. 265°和2. 12°。密封试验结果如表1 所示。试验结果表明,施工采用接头密封结构的密封性在设计偏角内可以满足现场要求。
表1 密封试验结果
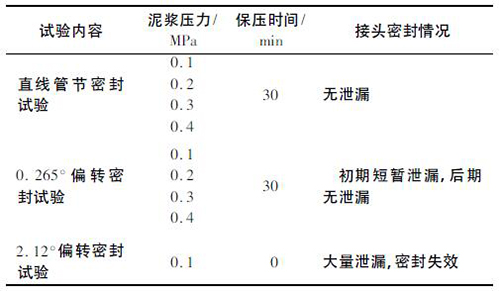
2. 5 复合地层顶管泥浆工艺
泥水平衡顶管施工必备2 类泥浆: 泥水平衡携渣泥浆和润滑减阻泥浆。对于一般单一地层顶管施工,泥浆工艺选择相对简单,但该管幕工程穿越多层复合软土地层,既有松散渗透性好的砂层,又有致密的黏土层,同时地下水含盐,对泥浆性能要求高。因此,需要根据不同地层的特性来分别制定与之配伍的泥浆工艺。
2. 5. 1 泥水平衡携渣泥浆
泥水平衡泥浆性能指标主要取决于地层的渗透性,渗透性越大,就要求泥浆的黏度越大。此外,考虑到含盐地下水对泥浆性能破坏较大,还需对浆液进行一定的抗盐处理。结合泥浆试验和现场使用效果,不同地层推荐的泥浆性能指标及配方如表2 所示。
表2 泥水平衡泥浆推荐表
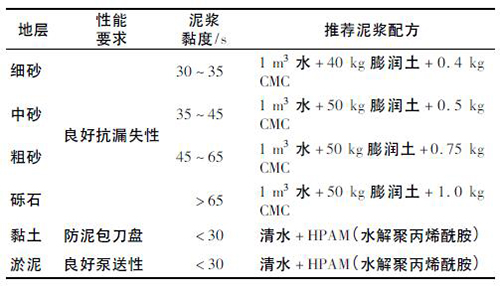
2. 5. 2 润滑减阻泥浆
与泥水平衡泥浆类似,润滑泥浆设计时主要考虑3 点: 1) 足够的黏度,在高渗透性砂层能保持泥浆长时间不漏失; 2) 良好触变性,使泥浆注入后能迅速变成凝胶状,有效堵塞砂层孔隙; 3) 泥浆应具有优良的抗盐水能力。
综合上述要求,在粗砂、砾砂层中,泥浆的马氏漏斗黏度应不低于60 s,最终试验确定的泥浆配方为1 m3淡水+ 50 kg 复合膨润土+ 0. 8 ~ 1 kg PAC - HV。该减阻泥浆配方对于致密黏土、淤泥质土均可适用,若地层渗透性较砂层更强,则考虑添加堵漏剂等材料。
以0 号试验管单位面积摩阻力曲线为例( 如图13所示) ,随着顶进距离的继续增加,泥浆的润滑性得到了较好的发挥,单位面积平均摩阻力稳定在1 kPa 以下,大大减小了顶管施工所需要的顶进力。
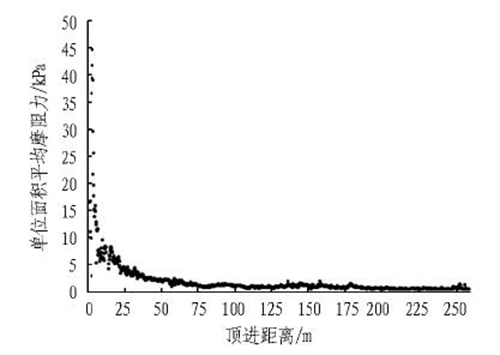
图13 0 号管单位面积摩阻力曲线
2. 6 障碍物处理及顶管应急处理技术
2. 6. 1 顶管障碍物处理技术
管幕上部顶管在穿越拱北口岸、澳门联检大楼及风雨廊过程中,遭遇大量建筑垃圾,包括混凝土块、钢筋、孤石等,造成顶进速度缓慢,并伴随出现钢筋短节堵塞泥浆管路等问题。因此,针对不同障碍物,提出如表3 所示的处理方法,并采取以下处理措施。
1) 根据顶力和刀盘旋转情况判断前方障碍物类型,根据情况适时调整顶进参数。
2) 进入风雨廊段后,加大泥浆比重,提高携渣能力,以便能携带出更多垃圾。
3) 根据排渣情况,安排专人及时检查管路是否堵塞,并及时清理,恢复顶进。
表3 顶管障碍物处理方案
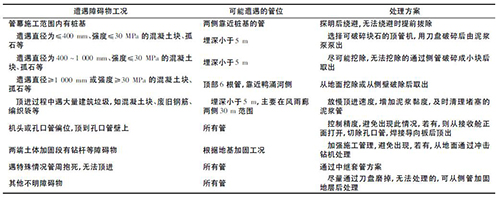
2. 6. 2 中继套管顶管机脱困技术
9 号顶管在顶进过程中遇到工作井突发涌水事故,为了控制地层水土流失,采取了注浆措施。期间9号顶管处于长时间停机状态,从而导致润滑泥浆大量流失,部分管节被土体及堵水浆液固结抱死,无法正常顶进。该顶管自东侧工作井始发,至西侧工作井接收,已累计顶进247. 945 m,剩余长度6. 6 m,此时,刀盘已穿过西工作井土体加固区,进入素混凝土墙约200 mm。
通过讨论筛选,最终研发出中继套管顶管机脱困技术[17],实施过程如图14 所示。将顶管机后方原有的第2 个和第3 个管节间F 型接头脱开,套入外径为1 000 mm的小直径管节; 小直径管节前端与原有第2节管节通过异形承插口连接,后端利用顶进油缸连接在后续抱死管节加强法兰上,小管节与原有第3 个管节之间设置2 道止水密封圈。

图14 中继顶进法示意图
脱困时,安装在小管节后方的顶进油缸以后续抱死管节为支撑,将前方的顶管机头连同原有第1 个和第2 个管节顶出,在原有第2 个和第3 个管节顶进分离后,2道密封圈防止地下水和泥浆进入管节内。最终顶管机顺利进入接收舱,实现脱困。
3 结论与讨论
1) 在类似拱北隧道高水压复合软土地层中进行顶管施工,泥水平衡顶管机是合理的选择,为实现在不同地层中高效掘进,宜配备复合刀盘。机械连接方式的钢管节不仅实现了钢管曲线顶进,而且采用的鹰嘴型橡胶圈满足现场0. 3 MPa 水压力的密封要求,但钢管节在曲线顶进条件下的受力特性及接头偏转对橡胶圈密封性的影响有待进一步研究。
2) 对于临海复合软土地层顶管施工,顶管泥浆的制备需考虑地层的特性,砂性地层泥浆以抗渗漏为主,黏性地层泥浆应具有防止泥包刀盘的性能,同时应注意泥浆的抗盐水侵蚀能力,要保证泥浆性能在长时间内保持稳定。
3) 工程创新提出的超小间距曲线顶管精度控制技术,不仅满足该管幕精度要求,也可为后续曲线顶管精确顶进提供技术依据。采用的泥水平衡钢套管接收舱实现了高水压复杂地质条件下顶管机安全接收,将成为高水压顶管接收施工的优选技术。中继套管顶进法通过在机头后方设置中继小管节,实现了在管节抱死情况下的机头脱困顶进。
摘自:隧道建设