0 引言
城市地铁建设因受到城市地面既有建筑及管线等影响,多采用暗挖法施工[1]。作为新奥法的一个分支,双侧壁导坑法已占据了重要位置[2 - 4],对第四纪地层特别是软土地层,对大断面隧道传统或常规多采用双侧壁,但对岩层有无必要及开挖方案值得探索。
国内学者对双侧壁导坑法也有很多研究,如软弱围岩开挖的地表沉降规律[5]; 双侧壁导洞出洞的技术处理方案[6]; 施工参数如支撑形式和开挖拆撑长度等方面的优化[7]; 通过数值模拟分析隧道围岩应力和位移特征等因素研究双侧壁导坑法[8]; 施工工艺及技术应用等研究[9]。实践证明: 双侧壁导坑法较为安全,但开挖分部较多,支撑支拆量大,不利于进度控制[10],留设核心岩柱法减少了导洞开挖个数及支撑支拆数量,加快施工进度[11],如重庆地铁车站采用全断面留设核心岩柱且作为初期支护应用[12]。本文以青岛市地铁一期工程( 3 号线) 太平角公园站- 延安三路站区间存车线大断面的设计及方案为依托,通过施工工法的优化与调整,结合监测数据可知,预留核心土开挖技术具有安全可靠、施工简化、节约成本及加快进度等优点。
1 工程概况
1. 1 工程位置与周边环境
青岛市地铁一期工程( 3 号线) 太平角公园站- 延安三路站区间位于香港西路下方,其中K5 +795. 864 ~ K6 + 000 里程段为单洞四线存车线大断面,开挖支护采用双侧壁导坑法( 2 层6 部) ,穿越新湛二路、东海一路与香港路的交会点; 北侧有光大银行、裕源大厦等高层建筑; 南侧局部有7 层以下的砖混结构建筑。该段隧道由延安三路站1 号风道西侧新增的横通道作为施工通道进行施工,平面位置关系见图1。
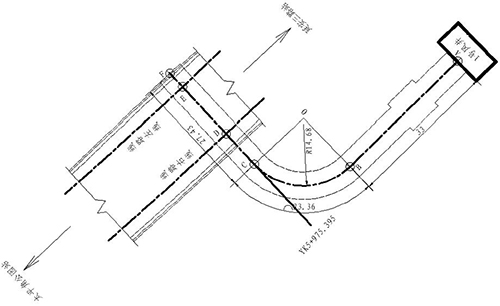
图1 存车线大断面施工平面位置图
1. 2 工程水文地质概况
存车线B2 断面隧道顶部埋深约18 m ,地面以下地质情况依次为素填土层,厚度为1. 0 ~ 1. 5 m,局部含砂黏土层0 ~ 2. 5 m,全风化花岗岩层0 ~ 1 m,强风化花岗岩层7 ~ 9 m,中风化花岗岩2. 7 ~ 7. 5 m,往下至隧道拱顶微风化花岗岩层1 ~ 5 m。隧道结构基本位于微风化花岗岩层,局部存在块状碎裂带。右线B2断面隧道顶部埋深约18. 5 m ,地面以下地质情况依次为杂填土层1. 2 ~ 2 m,局部含砂黏土层0 ~ 8. 7 m,局部粉质黏土层0 ~ 3. 5 m,全风化花岗岩层0 ~ 2 m,强风化花岗岩层3 ~ 20. 5 m,中风化花岗岩1. 5 ~ 7 m。隧道结构基本位于微风化、中风化花岗岩层,局部位于强风化花岗岩下压带。围岩分级为Ⅲ级。
1. 3 设计概况
B2 断面尺寸为宽21. 5 m,高13. 2 m,初期支护衬砌为350 mm 厚C25 喷射混凝土,主筋为25 的钢格栅,间距0. 5 m/榀,双层钢筋网8@ 200 mm × 200mm,22 砂浆锚杆、L = 3. 5 m、环向× 纵向=1 000 mm × 500 mm。二次衬砌为700 mm 厚C45、P10防水混凝土。B2 断面结构图见图2。
2 施工方法优化与调整
2. 1 双侧壁导坑6 部预留核心土开挖
2. 1. 1 优化后的施工开挖步序
双侧壁导坑预留核心土施工步序及要点如图3所示。先开挖1 部和2 部,再开挖3 部,先后错距不小于15 m,待上层施工完成后再施工下部4 部和5 部,中间预留核心岩柱结合后期二次衬砌施工进度逐步开挖。其中3 部采用台阶法开挖,上下台阶只预留一个循环进尺的步距,上台阶开挖支护完成后,下台阶立即跟进、完成开挖支护; 循环进尺为0. 75 m。施工过程中加强地层判定和施工监测管理工作,如有异常情况,及时采取措施,确保施工安全; 若监测数据出现异常时,及时在上部补强临时支撑加固。
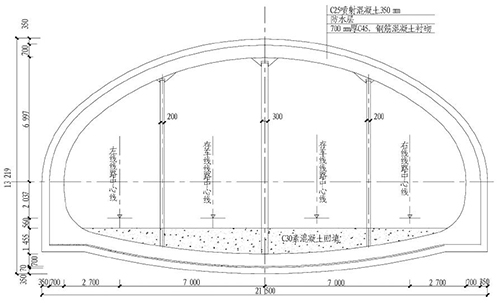
图2 B2 断面结构图
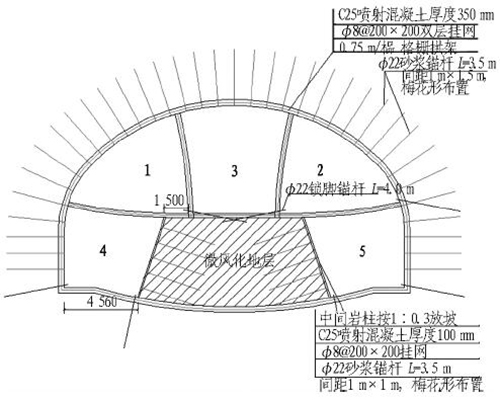
图3 施工顺序与分步方法示意图
与常规双侧壁导坑法[13]相比,施工工序相对简单,后续二次衬砌前拆撑范围小,且一次施作宽度较小,有利于隧道整体稳定性; 人工投入减少,利于施工进度控制,太延区间大断面开挖至衬砌结束共用时约13 个月,较采用原设计施工方法计划工期减少3 个月; 太延区间大断面较原设计施工方法费用约减少600 万元,此方案具有明显的施工优势。
2. 1. 2 施工参数
2. 1. 2. 1 爆破开挖参数
整个断面分为6 部钻爆开挖,设有掏槽眼、扩槽眼、掘进眼、周边眼和地板眼等,分别为1 -5 部及预留岩柱。
1 部和2 部爆破进尺设计按照750 mm/循环; 炸药单耗量1. 139 kg /m3,每次爆破量22. 52 m3 ; 毫秒管加6 发连接管及引爆管; 每循环共计124 发; 单段最大装药量4. 2 kg。
3 部由于断面高度较大( 7 419 mm) ,分上下台阶开挖。上台阶爆破进尺设计按照750 mm/循环; 炸药单耗量1. 29 kg /m3,每次爆破量11. 72 m3 ; 毫秒管加6发连接管及引爆管; 每循环共计62 发; 单段最大装药量3. 6 kg。下台阶爆破进尺设计按照1 000 mm/循环; 炸药单耗量0. 28 kg /m3,每次爆破量27. 67 m3 ; 毫秒管加6 发连接管及引爆管; 每循环共计47 发; 单段最大装药量2. 4 kg。
4 部和5 部爆破进尺设计按照750 mm/循环; 炸药单耗量0. 82 kg /m3,每次爆破量22. 63 m3 ; 毫秒管加6 发连接管及引爆管; 每循环共计72 发; 单段最大装药量3. 6 kg。
预留岩柱爆破进尺设计按照750 mm/循环; 炸药单耗量0. 15 kg /m3,每次爆破量60. 53 m3 ; 毫秒管加6发连接管及引爆管; 每循环共计45 发; 单段最大装药量6 kg。
2. 1. 2. 2 锁脚锚管( 杆) 参数
在每处拱脚位置布设2 根HRB400 的22、L =4. 0 m的锁脚锚杆,锁脚锚杆的孔内填塞水泥砂浆、锚杆尾端与钢架焊接牢固。
2. 1. 3 临时支撑拆除
临时支撑结合二次衬砌混凝土的施工顺序进行拆除,拆除时采用了人工辅助挖掘机( 带破碎头) ,先拆除混凝土及网片,再切割钢架; 每次拆除的长度为9m; 临时支撑拆除时保证先浇筑的混凝土强度达到设计强度要求[14]。
与双侧壁导坑预留核心土相比,常规双侧壁导洞法[13]拆撑需拆3 道临时仰拱,增加临时破除一层横向支撑施工工序; 施作衬砌仰拱过程需一次拆除2 道横向临时仰拱,增加拆撑施工安全风险,对初期支护衬砌结构稳定造成不利影响; 同时增加横向及竖向临时支撑架设施工作业,临时支撑影响后续支架搭设等施工的流水作业;最后临时支撑拆除亦是一项施工内容,延长施工工期。
预留核心岩柱6 部施工工法拆撑过程中施工下层临时中隔壁取消临时拱架,采用简单的锚网喷支护方法减小破除拱架的工作量,加快施工进度; 太延区间大断面采用预留核心岩柱6 部施工方法,充分利用预留核心岩柱,在下部边墙及拱顶衬砌施工中,使支架与坚实岩层接触,减小了支架搭设工程量的同时又降低拱顶衬砌施工高度,大大降低了施工安全风险; 同时避免了原设计施工方法中横向及竖向临时支撑架设的施工风险。
2. 2 二次衬砌施工
结构二次衬砌采用泵送模筑混凝土进行施工,模板采用900 mm × 1 500 mm 和300 mm × 1 500 mm 标准组合钢模板( 面板厚度t = 5 mm) ,支撑体系采用扣件式满堂支架。施工采用环向分部、纵向分组的方法进行。B2 断面结合断面形式、临时支撑位置和核心岩柱的留置及挖除方式,整个断面的衬砌施工环向按施工顺序共分两侧仰拱- 下部边墙- 上部边墙- 拱部-核心岩柱处仰拱5 个步骤。
2. 2. 1 核心岩柱两侧仰拱施工
见图4。
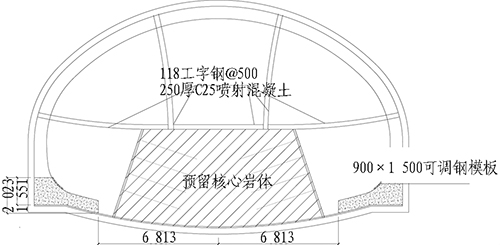
图4 核心岩柱两侧仰拱施工方法示意图( 单位: mm)
初期支护衬砌验收合格及接地施工完成后,按照纵向分组情况开始分段进行核心岩柱两侧仰拱的施工。本次施工高度为2. 023 m,在底部与核心岩柱之间用20 mm 厚胶木板进行封堵并加固牢固,与核心岩柱间空隙主要考虑防水板和钢筋的预留。
仰拱拆模后,对于仰拱与核心岩柱之间的空隙纵向每隔2 m 用C45 混凝土预制块填塞密实( 填塞长度为500 mm) ,预制块与核心岩体及衬砌混凝土之间的空隙用混凝土砂浆填塞,作为仰拱封闭前的临时支护措施。预制块为目前区间隧道衬砌施工时的预料加工制成,尺寸为500 mm × 200 mm × 100 mm。
2. 2. 2 下部边墙施工
仰拱施工完成后,拆除临时仰拱,搭设模板支架,施工下部边墙二次衬砌。本次施工高度为4. 272 m,采用300 mm ×1 500 mm 钢模板,每侧15 块。支撑系统采用600 mm × 600 mm × 600 mm 扣件式满堂支架,钢管为48 钢管,t =3. 2 mm。次龙骨采用48 钢管梳形木,间距500 mm,梳形木采用48 × 3. 2 钢管加工制作,每一组的各榀梳形木之间纵向用钢管连接成整体,梳形木与纵向主龙骨之间用铁丝捆扎牢固。为防止模板支架的纵向位移,可在模板支架两端架设斜向抛撑梳形木加工形式。主龙骨采用50 mm ×100 mm 方管。
2. 2. 3 上部边墙施工
下部边墙施工完成后,原钢管支架不拆除,模板和梳形木可根据拆模要求提前拆除,按图所示接高模板及支架施工上部边墙。施工高度为3. 717 m,模板均采用300 mm × 1 500 mm 钢模板,每侧20 块。模板支架及主次龙骨施工要求同下部边墙施工。
2. 2. 4 拱部施工
见图5。
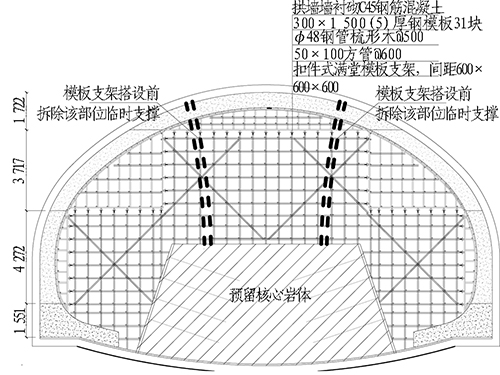
图5 拱部施工模板支架示意图( 单位: mm)
上部边墙施工完成后,混凝土达到设计强度后,如图5 所示拆除上部临时中隔壁,接长模板和支架,施工拱部衬砌结构。拱部弧度共使用31 块钢模板拼装而成,模板由两侧向中间依次拼装,在中线右侧有215mm 的空隙用2 mm 厚胶木板+ 方木与两侧钢模板拼接严密。模板支架及主次龙骨同2. 2. 2。
2. 2. 5 模板支架拆除及上部核心岩柱的挖除
根据同条件养护试件强度报告,待混凝土强度达到设计强度后由上至下拆除模板支架。
2. 2. 6 核心岩柱的开挖
采用松动爆破逐层挖除核心岩柱,每次爆破高度不大于1. 5 m,最后预留2. 5 m 采用分段的方法进行拆除并及时施工中间仰拱。后期核心岩体爆破挖除施工时须对已成型的混凝土和预留防水板、钢筋进行保护,具体措施如下。
1) 下部2. 5 m 范围核心岩体的拆除必须分段进行,一次拆除长度不小于每段的分组长度,采用跳段拆除的方法进行,须保证已封闭段仰拱混凝土强度达到设计强度后方可拆除其相邻段的核心岩体。
2) 采用松动爆破的方式进行核心岩体的挖除,严格按照爆破设计打眼装药,控制好爆破震动和飞石。
3) 爆破施工时须按要求设置炮被,炮被上边压工字钢等防止飞石。下部2. 5 m 范围核心岩体拆除时,还须在其两侧已施工完的仰拱混凝土部位铺设炮被,以防止飞石对已完成混凝土面的损坏。
4) 爆破施工前对两侧仰拱预留的防水板和接头钢筋用渣土或砂袋进行保护。
3 监控测量分析
监测数据主要取太延区间大断面预留核心岩柱地表沉降、太延区间主体结构洞内收敛、拱顶沉降和地表沉降的监测数据进行分析,具体统计数据如图6 -10 所示。
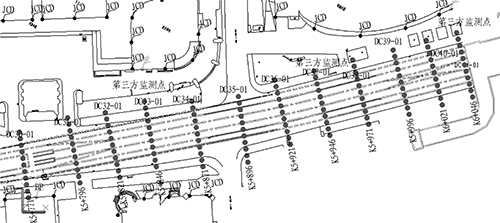
图6 地表沉降监测图
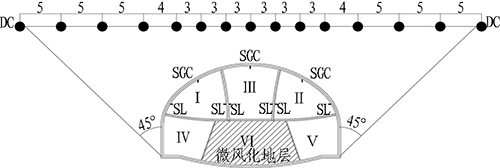
图7 监测点布置示意图( 单位: m)
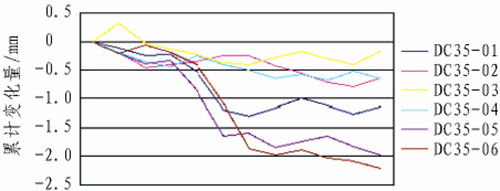
图8 地表沉降监测数据折线图
根据上述监测数据所示,可以说明采用双侧壁导坑预留岩柱6 步开挖法能达到支护要求,对城市地面影响较小,能满足安全质量生产的需要。该区段设地表监测点共11 排121 个,最大累计沉降点为DC39 - 06 ( K5 +996) ,-3. 21 mm; 拱顶沉降监测点共33 组33 个,最大累计沉降为SGC5 - 39( K5 + 996) ,- 2. 43 mm; 净空收敛监测点共55 组110 个,最大累计沉降量为SL5 - 36( K5 +921) ,-4. 83 mm。预留核心岩柱工法拆撑过程中,地表沉降累计量较小,最大累计沉降- 3. 21,初期支护衬砌结构监测数据稳定,所有数值均处于正常范围之内,没有异常情况发生,安全符合施工要求。
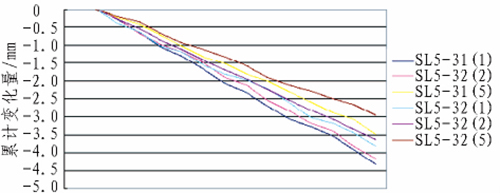
图9 收敛监测数据折线图
4 结论与探讨
通过对双侧壁导洞法进行优化与调整,采用预留核心岩柱施工技术,对比常规双侧壁导坑法,阐述地铁浅埋隧道开挖步序、爆破参数、支撑支拆、二次衬砌施作及监控测量等参数要点,得出结论如下。
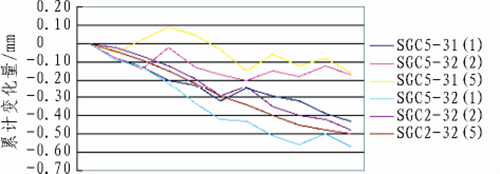
图10 拱顶沉降监测数据折线图
1) 简化了施工步序,减少了洞室开挖数量,加快了施工进度,太延区间大断面开挖至衬砌结束共用时约13 月,较原施工工法计划工期减少3 个月。
2) 预留核心岩柱法的后续二次衬砌前拆撑范围变小,且一次施作宽度变小,有利于隧道整体稳定性。
3) 拆撑的工程量减少,减少了对拱架等材料消耗,大大降低了人工和机械等成本,提高了施工效率,太延区间大断面较原施工工法费用节约约600 万。
4) 通过监测数据显示,地表沉降累计变化量较小,主体结构比较稳定,拱顶沉降基本可以忽略不计,通过与有关规范对比,认为太延区间存车段施工是安全的。
双侧壁预留核心岩柱法对施工进度控制、拆撑安全、成本降低具有重要的现实意义,但对后期岩柱拆除爆破是否对主体结构有影响及方法的适用范围还需进一步研究。
摘自:隧道建设